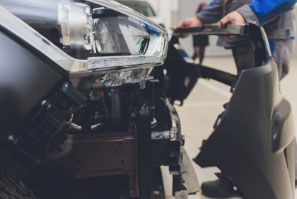
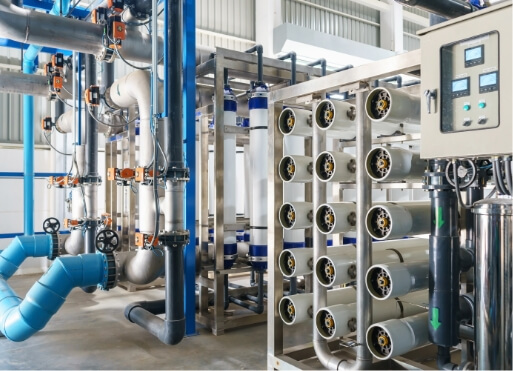
What are Obsolescence Management Services?
Obsolescence management entails services which are designed to help organizations control the threat of obsolescence. To achieve this, obsolescence management must be accounted for early in the development and design of a product, and it must continue through the exploitation and production phase. When done correctly, this form of management will maintain an ideal balance between ownership cost and operational availability, and functions by:
- The avoidance of numerous independent efforts for resolving an identical obsolescence problem which increases cost unnecessarily.
- The reduction of unacceptable losses that involve operational availability which come from overpriced redesign, and extended downtimes resulting from obsolete items that are no longer available.
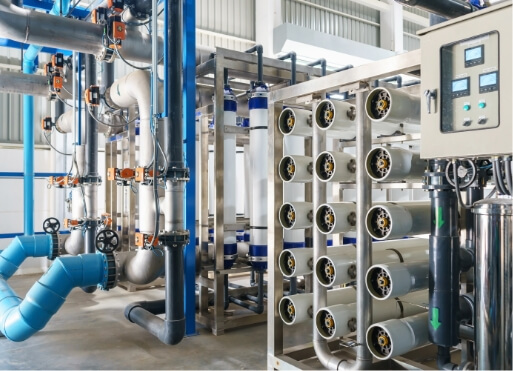
Why is Obsolescence Management Important?
This form of management is essential because it is continuous from product conception to production. For instance, during the conceptual stage, the company will formulate technical and functional requirements for a product. At this time, obsolescence management should be concisely defined as one of the essential activities within its technical and functional requirements.
During the contractual stage, conditions must be established which lay the foundation for planning, resolution, mitigation and analysis. Depending on contractual conditions, the TLMP (Through Life Management Plan) has to be made in a manner that includes specific components along with risk assessments at the product level.
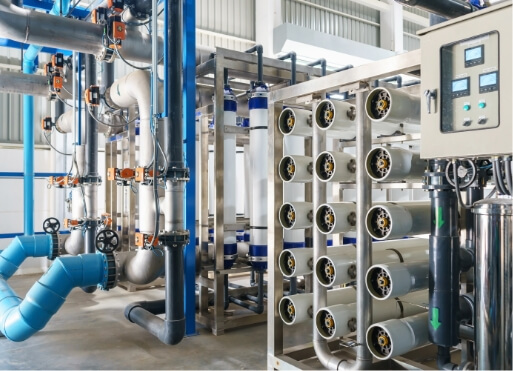
When are Obsolescence Management Services needed?
Obsolescence management is also a necessity during the design stage, particularly for post conceptualization. Within the structure, it must be further divided into subsystems. You must also perform parts selection where you will choose components which are suitable for your product’s finalized design. This process must be done carefully with an ideal balance between component quality and cost, because if you lower the grade of the components you might sacrifice functionality and system tolerance.
During the production stage, component availability must be assessed and finalized. The agency for production must ensure that component support is made available throughout its product life, and risk assessments should be performed to ascertain component risk with regard to obsolescence.
Part selection is influenced by many factors, like environment conditions, stress tolerance, standardization, the desired dimensions, planned product function and ruggedization. Obsolescence management involves identifying obsolete components, impact analysis, and the corrective action that needs to be taken and design release, which involves releasing the proper design to market.
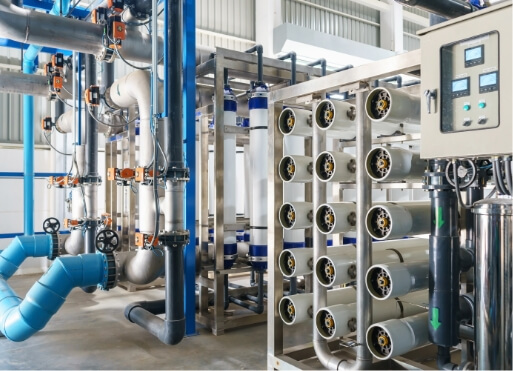
Why hire ReLogic Research for Obsolescence Management Services?
We perform risk assessment for all products which occur during specific time intervals. Based on these assessments, we will help you develop a highly efficient approach that can be applied to minimize obsolescence.
For more information about our obsolescence management services, you can call us at 256-713-7401 or fill out this online form.
Purpose Of Obsolescence Management
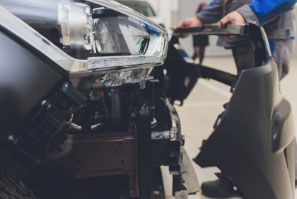
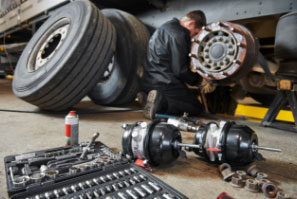
Parts Service Or Repair
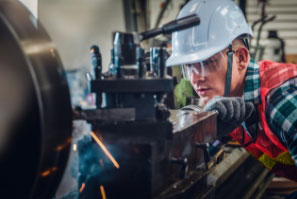
Parts Improvement
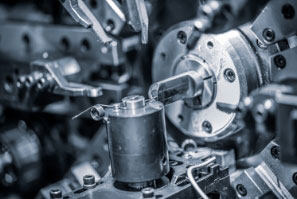